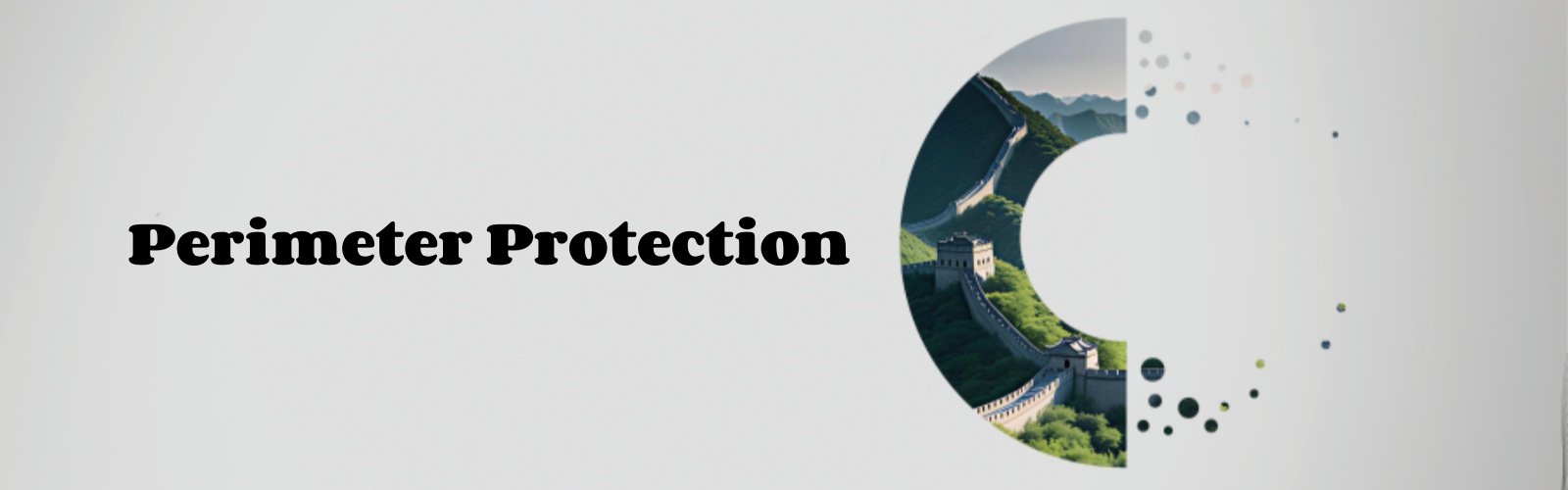
Fence manufacturing process, core technology, and quality control:
1. Post of forming technology
1.1 Cutting process
High speed precision punching machines are used for opening, installing, and connecting slots in column materials. The punching machine has a tonnage of 80 tons and is controlled by a stepper feeding PLC to ensure accurate spacing between the connecting slots.
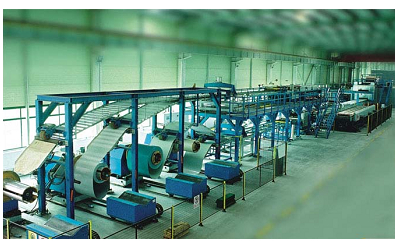
1.2 Cold rolling forming technology
Adopting the most advanced non-destructive cold rolling forming equipment in China for the forming of columns. The 95KW drive motor drives the molding mold for 36 passes, ensuring the smooth and precise positioning of the column surface and angles.

1.3 Plate Connection Technology
The connection dots derived from the manufacturing technology of the German automotive industry can achieve a perfect connection between two layers of components. The optimal connection between two or more layers of boards of different thicknesses and materials can be achieved without the need for heating or accessories. There are no requirements for the surface of the board, and the connection should not damage the original coating or paint layer.
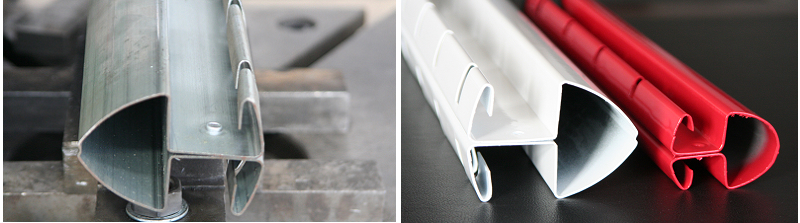
2. Mesh of forming technology
2.1 Cold drawn steel wire process
The high-strength steel wire production equipment used for mesh welding comes from the Austrian RIHR company, and the cold drawing and drawing process synchronized with the world effectively ensures the tensile strength, roundness, and high production capacity of the steel wire.
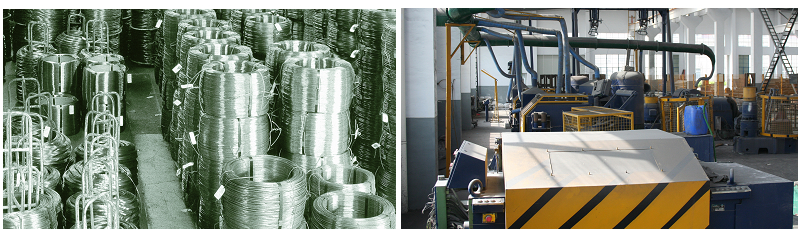
2.2 Mesh welding technology
The most advanced steel bar welding mesh forming equipment in China is used for welding and forming mesh sheets: the longitudinal wire rod is fed and straightened twice to continuously and smoothly produce mesh sheets; Horizontal strong magnetic positioning and automatic trimming of burrs ensure that the mesh is neat; PLC fully automatic control ensures that the mesh length is automatically cut and leveled, and the output length can be set; The servo motor drive ensures the output accuracy of the horizontal grid and can be adjusted arbitrarily; The microcomputer welding controller controls the thyristor to ensure the depth of indentation of the solder joint, the roundness of the solder edge, and the strength of the solder joint.
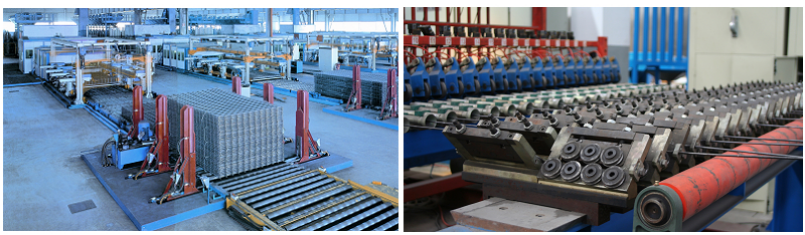
2.3 Strengthening groove stamping process
A specialized integrated strengthening groove bending mold for large tonnage hydraulic bending equipment is used for the pressing and strengthening groove shaping of mesh sheets; A pressure of 160 tons causes the bending to be flat and without recovery; A 4-meter workbench can process mesh within 3 meters.
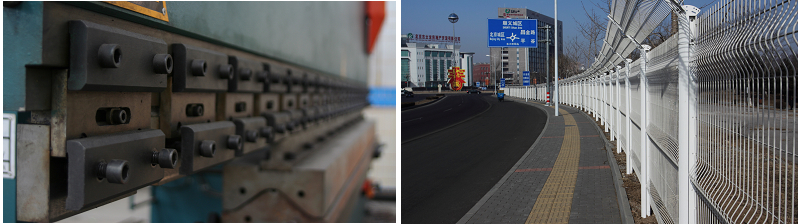
3. Raw material technology
3.1 Quality control in the procurement of raw materials, components, and semi-finished products is key to ensuring the quality of finished products. During the procurement process, our company strictly adheres to national and international standards for material technical performance based on the principles of high quality and good price, specified material materials, professional manufacturers, production process supervision, and qualified acceptance delivery. The columns are made of 1.2mm high-quality double-sided galvanized cold-rolled sheet, with a hot-dip galvanizing amount of ≥ 120kg; The steel wire adopts high-purity low-carbon high-speed wire specifically designed for wire drawing, and the sulfur and phosphorus content in the steel does not exceed 0.035; The anti pull design of the accessory (column top cover) is made of special engineering plastic injection molding, which has a long service life.
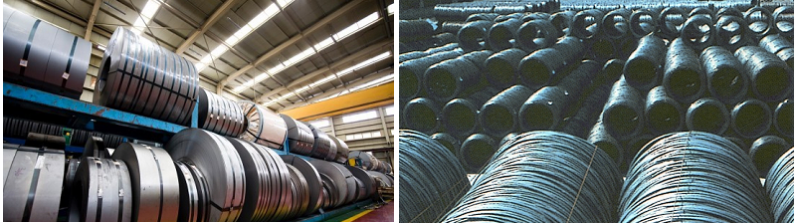
4. Surface treatment and coating technology
4.1 Main equipment
The coating production line owned by the company is provided by the world’s third ranked coating professional company. The coating line integrates German pre-treatment technology, American coating technology, and Italian heat exchange technology. The world’s leading level of coating equipment and technology ensures the coating quality of products at zero distance from the world. All components of the bidding product have undergone over three layers of anti-corrosion treatment, with super strong corrosion resistance and a quality assurance period of more than 10 years.
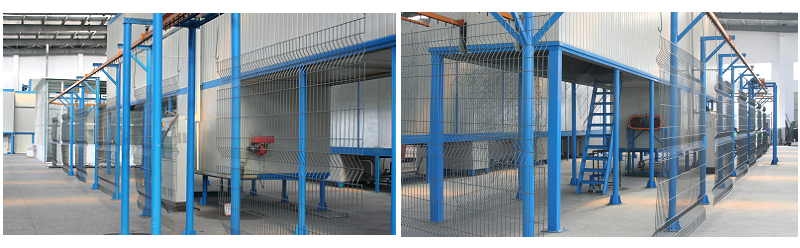
4.2 Phosphating film process (zinc based phosphating)
The use of the unique zinc based phosphating technology in the fence coating process is the core technology of the coating process: the zinc based phosphating film maximizes the adhesion between the polyester coating and the substrate, ensuring extraordinary anti-corrosion quality.
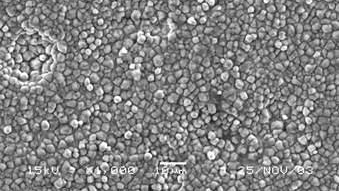
4.3 Schematic Table of Anti corrosion Texture of Coatings
Coating process | Outer coating | Inner coating | Base material |
![]() | High end PE coating process in the United States (with strong UV resistance and color stability) | German pre-treatment process and zinc rich phosphating layer (corrosion-resistant+increases substrate and coating adhesion) | High strength hot-dip galvanized steel wire, double-sided hot-dip galvanized high-quality all steel column |
4.4 Table of Technical Parameters for Surface Coating
Test project | Test method | Actual measured values of surface coating |
---|---|---|
Film thickness: | ISO2360 | ≥100μ |
Grid adhesion: | ISO2490 | 0 |
Impact test 20 inch pounds: | ASTMD2794 | No deep or substrate cracks |
Weatherability: | EN20105-A02 | ≥ 4 |
Photoaging: | ENISO105-B02 | ≥ 7 |
Resistant to humidity for 1000 hours | ISO6270-1 | Maximum foaming 1mm |
Salt spray resistance for 1000 hours | ISO9227 | Maximum subsurface corrosion 1mm |
5. Quality control
5.1 The company strictly controls every aspect of product production, processing, and manufacturing according to the established quality system and standards, strengthens the testing of raw materials and product manufacturing processes, and ensures the provision of high-quality products.
5.2 Production Process
5.2.1 Column production process: raw materials (hot-dip galvanized/aluminum zinc coated steel coils) – longitudinal cutting with fixed width and unwinding – opening installation groove – rolling forming – cutting to fixed length – precision cutting with fixed length – matching process holes – deburring – loading – degreasing – cleaning – phosphating – pure water cleaning – drying – spraying – curing – unloading – packaging – finished product
5.2.2 Mesh production process: Raw material (Q195 hot-rolled high wire rod) – Cold drawn drawing – Hot dip galvanizing – Small plate galvanized coil – Wire rod/straight rod feeding Welding net – trimming – punching – pressing strengthening groove – upper part – degreasing – cleaning – phosphating – pure water cleaning – drying – spraying – curing – lower part – packaging – finished product
5.3 Product Quality Control Form
5.4 Table of Technical Parameters for Surface Coating
Item | Reference standards | Standard value |
---|---|---|
Mesh Panel | BS EN 10223-7 BS EN 10244-2 GB343-94、ASTM A185 | The allowable deviation of steel wire diameter after plastic molding is ± 0.05mm, and the allowable deviation of mesh size is 3mm Steel wire tensile strength ≥ 550Mpa, welding point shear resistance ≥ 3000N Hot dip galvanizing amount of mesh ≥ 120g |
Post | BS EN 10346 GB700 | Post tensile strength ≥ 450Mpa, post curvature ≤ 1.5mm/m Post hot-dip galvanizing amount ≥ 120g |
Organic Coating | BS EN 10245-4 | Coating thickness ≥ 60um |
Fence manufacturing process, core technology, and quality control
1. Pipe of forming technology
1.1 Pipe making process
Automated unwinding, high-frequency welding, and pipe forming equipment can achieve high-quality and efficient processing and manufacturing of pipes.
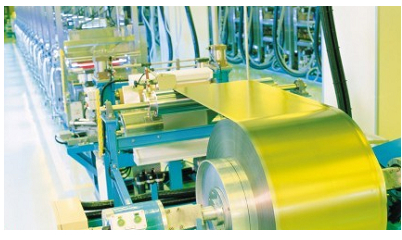
1.2 Cutting process
High precision band sawing machine is used for cutting pipes to a fixed length. The 280mm worktable can process large workpieces or multiple workpieces at once, reducing machining errors of workpieces.
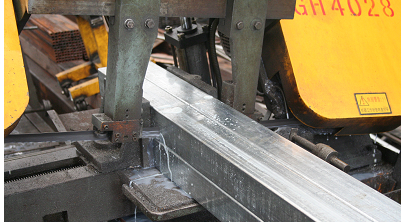
1.3 Stamping process
Using specialized stamping equipment for the processing of process holes in pipes, in conjunction with stamping molds provided by experienced domestic mold manufacturers, the precision of pipe process hole diameters is fully guaranteed.
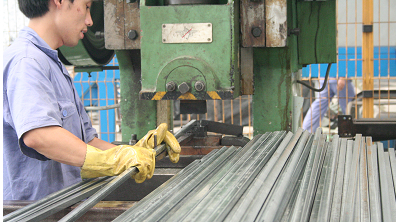
2. Raw material technology
2.1 Quality control in the procurement of raw materials, components, and semi-finished products is key to ensuring the quality of finished products. During the procurement process, our company strictly adheres to national and international standards for material technical performance based on the principles of high quality and good price, specified material materials, professional manufacturers, production process supervision, and qualified acceptance delivery.
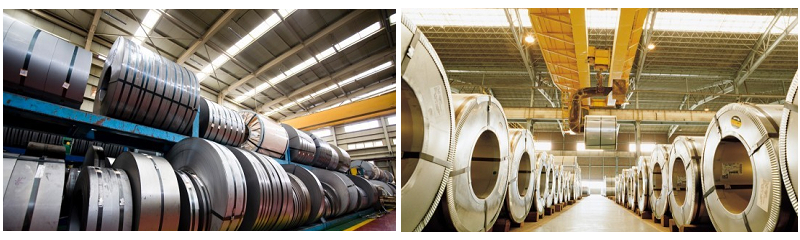
3. Surface treatment and coating technology
3.1 Production Equipment The coating assembly line owned by the company is provided by the world’s third ranked coating professional company. The entire assembly line integrates German pre-treatment technology, American coating technology, and Italian heat exchange technology. The world’s leading level of coating equipment and technology ensures the coating quality of products at zero distance from the world. All components of the quoted fence product have undergone over three layers of anti-corrosion treatment, possessing super strong corrosion resistance and a quality assurance period of more than 10 years.
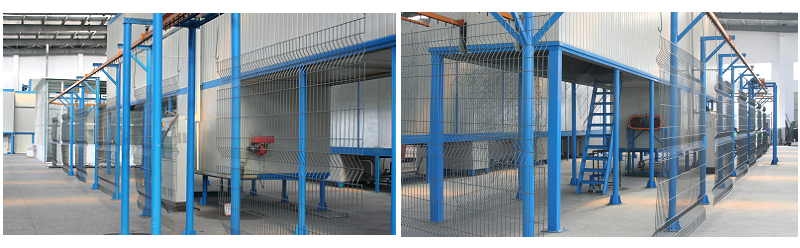
3.2 Phosphating film process (zinc based phosphating)
The use of the unique zinc based phosphating technology in the surface coating process of fence products is the core technology of the coating process: the zinc based phosphating film maximizes the adhesion between the polyester coating and the substrate, ensuring extraordinary anti-corrosion quality.
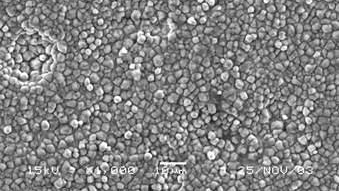
3.3 Schematic Table of Anti corrosion Texture of Coatings
Coating process | Outer coating | Inner coating | Base material |
![]() | High end PE coating process in the United States (with strong UV resistance and color stability) | German pre-treatment process and zinc rich phosphating layer (corrosion-resistant+increases substrate and coating adhesion) | High strength hot-dip galvanized steel wire, double-sided hot-dip galvanized high-quality all steel column |
3.4 Table of Technical Parameters for Surface Coating
Test project | Test method | Actual measured values of surface coating |
---|---|---|
Film thickness: | ISO2360 | ≥100μ |
Grid adhesion: | ISO2490 | 0 |
Impact test 20 inch pounds: | ASTMD2794 | No deep or substrate cracks |
Weatherability: | EN20105-A02 | ≥ 4 |
Photoaging: | ENISO105-B02 | ≥ 7 |
Resistant to humidity for 1000 hours | ISO6270-1 | Maximum foaming 1mm |
Salt spray resistance for 1000 hours | ISO9227 | Maximum subsurface corrosion 1mm |
4. Quality control
4.1 The company strictly controls every aspect of product production, processing, and manufacturing according to the established ISO9001:2008 quality system, strengthens the testing of raw materials and product manufacturing processes, and ensures the provision of high-quality products.
4.2 Production Process
4.2.1 Production process: Raw materials (hot-dip galvanized/aluminum zinc coated steel coils) – longitudinal cutting with fixed width and unwinding – opening installation groove – rolling forming – cutting to fixed length – precision cutting with fixed length – matching process holes – deburring – loading – degreasing – cleaning – phosphating – pure water cleaning – drying – spraying – curing – unloading – packaging – finished product
4.3 Product Quality Control Form
Item | Reference standards | Standard value |
---|---|---|
Hot dip galvanized coil | GB700 | Thickness tolerance ± 0.05mm, tensile strength ≥ 450Mpa |
Substrate anti-corrosion | BS EN 10346 | Hot dip galvanizing amount ≥ 120g |
Organic Coating | BS EN 10245-4 | Phosphating film thickness 5-8um, coating thickness ≥ 60um |
Manufacturing process, core technology, and quality control of sliding gates/swing gates
1. Gate body of forming technology
1.1 Gate bottom beam forming technology
The industry’s unique automated cold bending equipment and non-destructive cold bending technology for large section profiles are used for the one-time forming of the C-type high-strength manganese steel bottom beam of the sliding door body.

1.2 Welding deformation control technology for gate body
The welding and forming of the gate body adopts a fully digital controlled pulse MIG/MAG welding machine, which has excellent welding performance and high-precision control function, ensuring the welding quality of the gate; The unique welding deformation control technology of the gate body ensures the structural quality of the electric sliding gate.
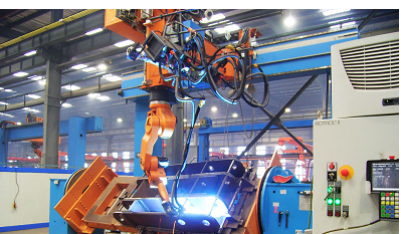
1.3 Pipe cutting technology
High precision band sawing machine is used for cutting pipes to a fixed length. The 280mm wide worktable can process multiple workpieces at once, reducing machining errors and improving the efficiency of workpiece processing and manufacturing.
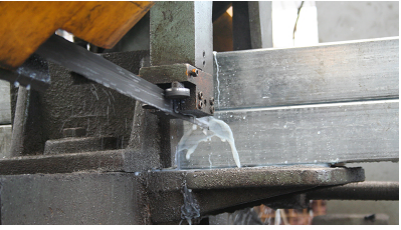
2. Raw material technology
The quality control of raw materials, components, and semi-finished products procurement is the key to ensuring the quality of finished products. In the procurement process, the principles of high quality and good price, designated material materials, professional manufacturers, production process supervision, and qualified acceptance delivery are strictly followed, and national and international standards for material technical performance are strictly implemented.
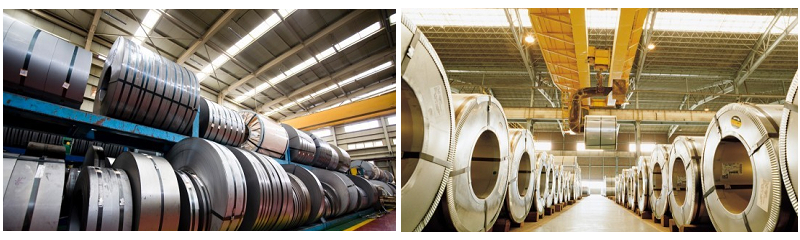
3. Drive system technology
The cantilever trackless electric sliding gate adopts a special motor imported from Italy FAAC, and the world-class drive system technology ensures the good quality and extraordinary service life of the sliding gate.
3.1 Comprehensive safety: The special oil immersed anti extrusion dual disc clutch can adjust thrust from 0 to 110 daN. Due to the irreversibility of the motor, there is no need for an electric lock. During a power outage, the door can be manually opened/closed using a customized release key operated release device.
3.2 Long lifespan: The mechanical components are continuously and completely lubricated with oil and are housed in a highly pressure resistant aluminum alloy shell, ensuring long-term use of the equipment.
3.3 High reliability: A safe electronic device, all commands are issued by a highly reliable microprocessor, using electromagnetic induction limit, and the door body stop position is precise.
3.4 Simple and convenient: The control board is installed inside the gear motor, making installation quick and efficient.
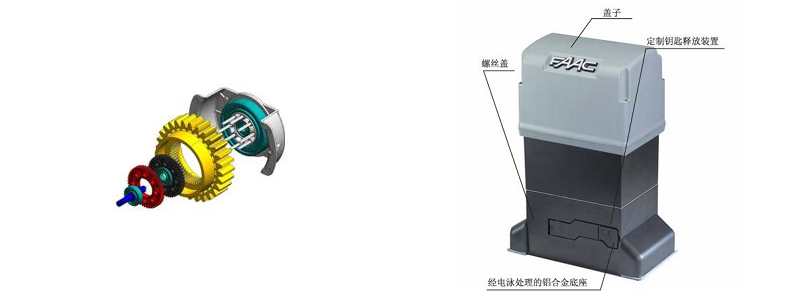
4. Gate surface treatment and coating technology
4.1 Pre treatment process and technology
The pre-treatment process and technology of the door body adopt shot blasting and hot spray zinc technology: large-scale specialized shot blasting and hot spray zinc equipment provide a basic guarantee for the extraordinary corrosion resistance of the finished door body.
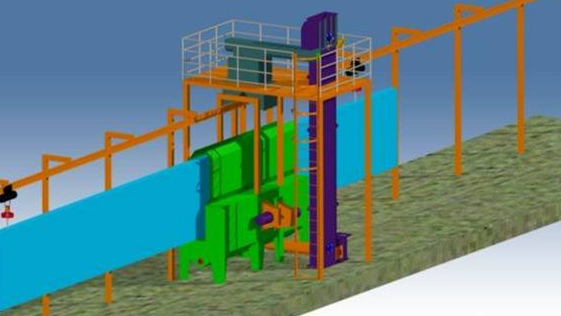
4.2 Gate Coating Process
4.2.1 Coating Equipment
The only fully automatic coating production line for heavy-duty workpieces in the domestic industry is used for the surface coating process of door bodies: 9-station pre-treatment shower tank (de esterification, cleaning, surface adjustment, phosphating, re cleaning, pure water cleaning) and German Henkel surface treatment materials achieve cleaning of the workpiece surface and thickness control of the phosphating film, ensuring the bonding rate between the coating and the substrate; The 6-station electrostatic powder spray gun from American Noxin Company evenly distributes the coating on the surface of the workpiece and effectively controls the coating thickness. The 300000 kcal Italian Riyalu combustion heat exchanger ensures the temperature energy required for solidification leveling. The heavy rail conveyor and stepless frequency conversion speed control ensure smooth and continuous production of the workpiece, reducing the quality difference of the entire batch of products.
4.2.2 Phosphating film process (zinc based phosphating)
The use of the unique zinc based phosphating technology in the door coating process is the core technology of the coating process: the zinc based phosphating film maximizes the adhesion between the polyester coating and the substrate, ensuring extraordinary anti-corrosion quality.
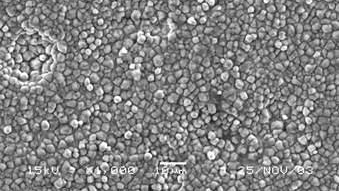
4.2.3 Schematic Table of Anti corrosion Texture of Gate Coating
Coating process | Outer coating | Inner coating | Base material |
![]() | High end PE coating process in the United States (with strong UV resistance and color stability) | German pre-treatment process and zinc rich phosphating layer (corrosion-resistant+increases substrate and coating adhesion) | High strength hot-dip galvanized steel wire, double-sided hot-dip galvanized high-quality all steel column |
4.2.4 Technical parameter table for gate surface coating
Test project | Test method | 29/49 Series High Gloss Surface |
---|---|---|
Film thickness: | ISO2360 | ≥100μ |
Grid adhesion: | ISO2490 | 0 |
Impact test 20 inch pounds: | ASTMD2794 | No deep or substrate cracks |
Weatherability: | EN20105-A02 | ≥ 4 |
Photoaging: | ENISO105-B02 | ≥ 7 |
Resistant to humidity for 1000 hours | ISO6270-1 | Maximum foaming 1mm |
5. Quality Control
5.2 Production Process
• Gate Body Forming: Raw materials (manganese steel plate/galvanized steel coil) → Slitting to width and uncoiling → Rolling and forming → Cutting to length → Precision cutting → Welding and forming → Grinding → Hole punching for accessories → Pre-commissioning
• Gate Body Pre-treatment and Coating: Formed gate body → Shot blasting for rust removal → Hot-dip galvanizing → Hanging parts → Oil removal → Cleaning → Phosphating → Purified water cleaning → Drying → Spraying → Curing → Removing parts → Finished gate body
• Gate Body/Motor/Accessories: Assembly of accessory components → Testing and inspection → Packaging and storage
5.3 Product Quality Control Table
Item | Reference standards | Standard value |
---|---|---|
Hot dip galvanized coil | GB700 | Thickness tolerance ± 0.05mm, tensile strength ≥ 650Mpa |
Substrate anti-corrosion | BS EN 10346 | Hot dip galvanizing amount ≥ 220g |
Organic Coating | BS EN 10245-4 | Phosphating film thickness 6um, coating thickness ≥ 60um |
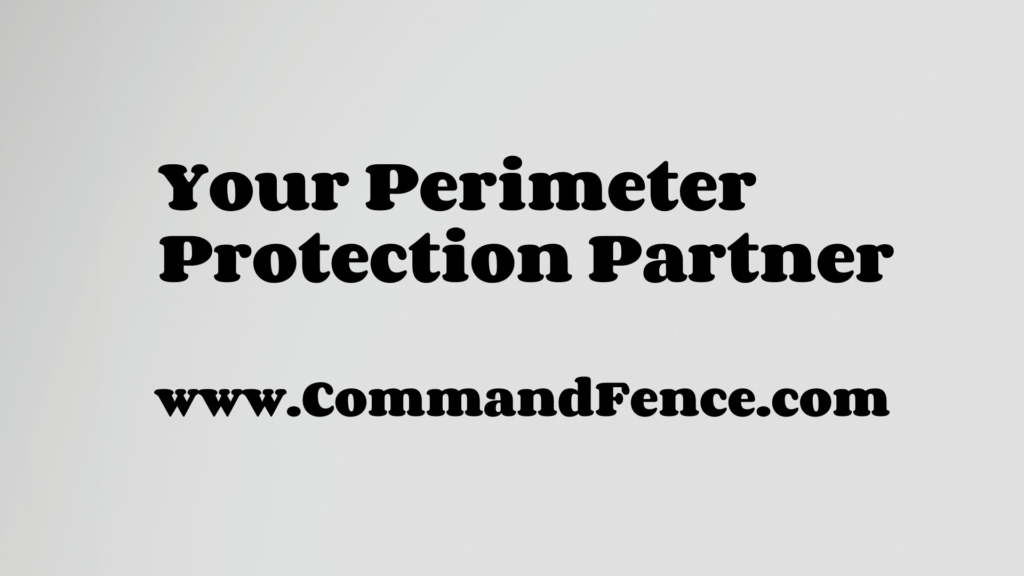